We have seen a new era in automobile propulsion recently with the introduction of electric cars. What was once fossil fuel based is fast approaching a clean, rechargeable battery design. Like any new development this introduces the need for new testing practices.
Advances in technology always bring new challenges in manufacturing as well as testing. The new, higher efficiency, longer life batteries also come with tighter leak tolerances. All aspects of manufacturing must be exact to ensure safe, reliable and long lasting performance.
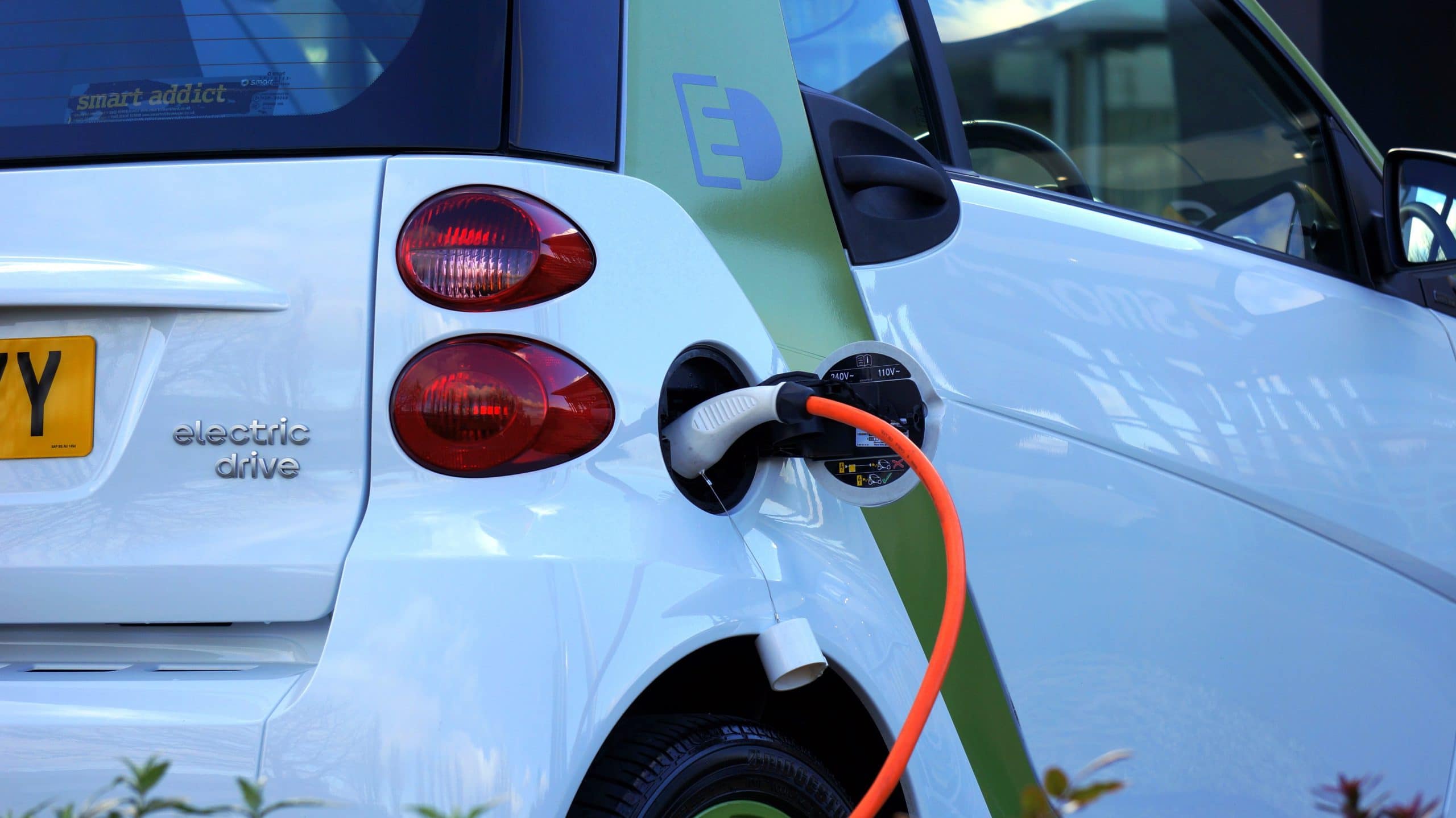
There is high leak tightness requirement for the lithium ion battery. The electrolyte of this battery is not only toxic but also hazardous and when in contact with air it will cause a fire. Also if air/humidity dilutes the electrolyte it will compromise performance of the battery. This is why leak testing is so important for this type of battery. This concept holds true (and more so) for hybrid batteries. Not only does water ingress dilute the chemical reaction, causing less powerful output, it also creates a safety issue with the Li-ion battery. This means the testing of these batteries is crucial to ensure safe, reliable operation.
There are three major components to a hybrid battery: the cell, the module and the pack. The cell/single battery is the smallest component, grouped or combined to form a single module. The modules are then grouped together to form a complete pack. Each of these components are leak tested against different leak specifications. Each of these specifications are dependent on the size, function and capability of the component or specification.
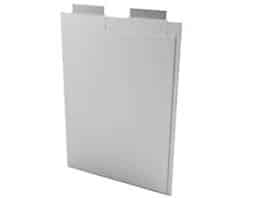
The cell is small (can be square as shown below or cylindrical) and is the first component of a battery pack. Therefore, it is tested to the tightest tolerance. In several industries test tolerances tend to grow as component levels increase. This method of testing comes from a basis that as you test components the final assemblies need only look for assembly defects, not component level defects. Typical leak specifications for cells are about 10-5sccs or mBar liter/sec.
These cells are grouped to form a module. Utilizing an electrical connection, the modules are then also grouped. This allows for the module packs to take several form factors to fit different vehicle models. A typical leak rate for a module application would be in the range of 10-3 sccs or mBar liter/sec.
The modules are then grouped into a pack. This pack consists of an electronic controller, the requirement modules, the connections for the vehicle and the coolant circuit. This pack is then leak tested for water ingress protection (IP67) at a leak rate of approximately10 SCCM. Due to the large size of this application, we recommend using low pressure or vacuum to ensure the packs are not damaged. For this application our model IPE2 would be the recommended instrument for testing. In addition, we can also test the coolant circuit. Hybrid coolant systems are generally the same as a standard vehicle coolant system with a similar leak specification. The volume of this application is small and only consists of about 2-4 liters of volume.
Cell Leak Testing
For a cell leak test application, the part size and leak rate are small. This poses a challenge. Tracer gas leak test methods would be an option, however the part does not easily allow for the insertion of the tracer (helium) gas. If we can insert the gas, we can achieve the desired sensitivity level. If we are unable to insert the tracer gas, Mass Extraction would be the next best option. It requires no tracer gas and will allow us to achieve our desired sensitivity level.
How the System Works
The operator places a cell into a small chamber and closes a lid over it. The system evacuates the air out of the chamber down to only a few torr of vacuum. Next, the system measures the air/gas that escapes from the cell and compares it to the “setpoint” established by predetermined leak limits. If the gas flow is less than the limit, it is accepted and passed as a good part. If the gas flow exceeds the limit, the part is rejected and removed from production.
Module Leak Testing
The second part of the battery leak testing process is the module leak test. If the size of the module is reasonable and the leak specification is large enough, this test can be performed without difficulty and complexity. These modules are quality built and can withstand higher pressures. This allows us to perform tests at pressures of about 20-30 psig. The connections to the module offer a good avenue for pressurization of the inside of the unit which will provide us with the best test results.
The volume of the module is small to medium in size (2-4 liters), the leak specification is large, and we can pressurize the inside. Because of this a few methods of testing are available. Tracer gas can be used and would provide great sensitivity results as well as a quick test speed. One downside to this test is the associated cost of the gas itself (most commonly helium). Micro flow technology is also a good choice since it has the sensitivity and the measurement accuracy necessary without the added cost of a tracer gas.
HMS Leak Testing
For tracer gas leak testing, Pfeiffer Vacuum offers an ASM340. Its high speed, measurement accuracy and stability make it well suited for automotive applications like these. The ASM340 also includes a slower, sniffer mode best used for offline and audit testing. In addition to the relatively fast speed, this method also gives the user the capability of detecting the location of the leak for repair bays and rework stations.
Pack Leak Testing
Packs come in all shapes and sizes due to their requirement to fit different car platforms and profiles. The pack leak test takes place when the modules are placed into a housing (either plastic or metal) and assembled for insertion into the vehicle. The pack can be very large and can contain air volumes of several hundred liters. The large surface area of the pack also restricts the pressure or vacuum limits it can withstand without getting damaged. Therefore, the leak test parameters are for low pressure or vacuum testing.
Micro Flow Leak Testing
If test times of 3-5 minutes are within your target for your pack test and you do not need to locate the leak, then ATC’s model IPE2 would be an excellent solution. The simplicity of the test makes it easy to implement and easy to maintain. The IPE2 is our industrial hardened instrument with flexibility to test large volume parts like packs with extreme accuracy using only air (in either vacuum or pressure tests). With its integrated electronic pressure controllers and micro flow technology, it has the unique ability to test larger parts faster than other methods like pressure decay. After sealing all connectors and vents, pressurize or pull a vacuum on the part to the necessary test range. You then measure the air flow of the leak. There are no chambers required nor tracer gas insertion and removal necessary. The IPE2 has excellent sensitivity and can measure a 10-20 sccm leak rate. No daily calibration is required, and the system has a built-in verification orifice so you can validate the test without fear of making poor test decisions.
Coolant Circuit Leak Test
Batteries can create a significant amount of heat when charging and discharging. Multiply this by several decades when referring to these massive battery packs used in hybrid vehicles. For these reasons, the coolant circuit for these packs must be leak tested and measured accurately and with repeatability.
The battery packs will require a cooling circuit using the same ethylene glycol and water mixture for conductance. This same system has been used for several years in the automotive industry and the leak specification is well defined and validated. The variable for packs is the volume of the coolant and this is less than the standard coolant circuit for a gas engine.
This test can be measured with our model E2 micro flow instrument. The test circuit is a few liters in volume, the connections and connection area are rigid, and the leak specification is around 10 sccm. The model E2 offers the same measurement stability and accuracy as the module leak test but will be faster than other air test methods, allowing less stations or test stands.
Pfeiffer Vacuum and ATC can offer you the right tester according to your application. Our dedicated team of experts are knowledgeable in leak testing and will guide you to the right product for your needs. Whether it is air or tracer gas based, we have the tools and equipment to satisfy your test requirements.