Container Closure Integrity Testing of Pouches is common across many industries. Several products we use on a daily basis get packaged in foil pouches, some of these include:
- Wipes
- Swabs
- Syringes
- Medical Devices
- Testing Strips
- Infant Nutrition
- Eye-Droppers
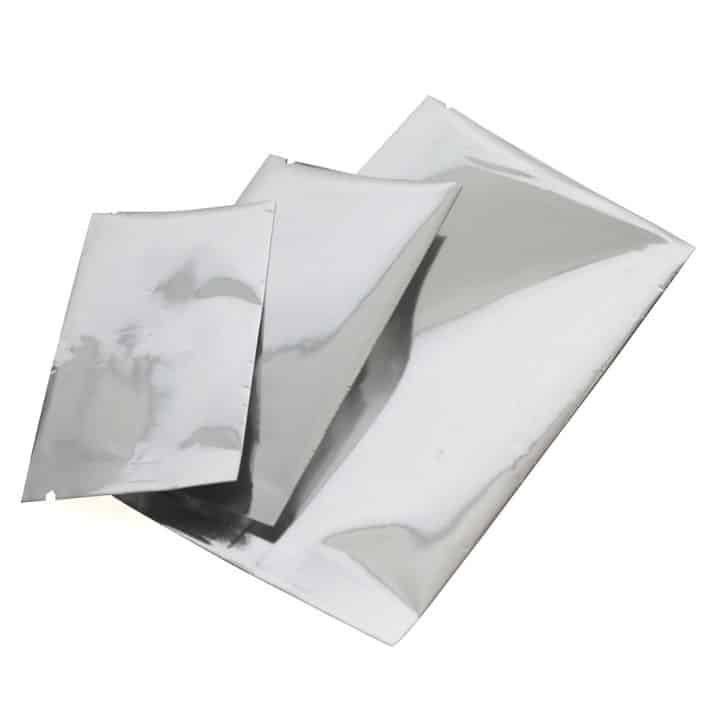
Foil pouches can vary in size, coating material, contents and testing requirements. Container tightness is generally described by a diameter of a sharp-edged hole-size/defect in microns. For help determining an appropriate tightness specification please see our CCIT Services article.
Most pouch tightness specifications range from 5 to 50-micron sharp edged defect size. For these applications we recommend Pfeiffer Vacuum’s VE2 or ME4 micro-flow vacuum tester. Combined with a customer test chamber you can be sure you have a reliable and cost effective test method.
VE2
Pfeiffer Vacuum’s most popular mass extraction test instrument. The VE2 has built-in quick fill for higher throughput.
Some key highlights about the VE2/ME4 micro-flow test method are
- Quantitative Measurements
- Non-Destructive Tests
- Deterministic Results
- Repeatability
- 25% to 50% faster than decay test methods
Dye Ingress in comparison limits tests to roughly 20-microns or higher. Dye Ingress is also messy, qualitative, stochastic and destructive.
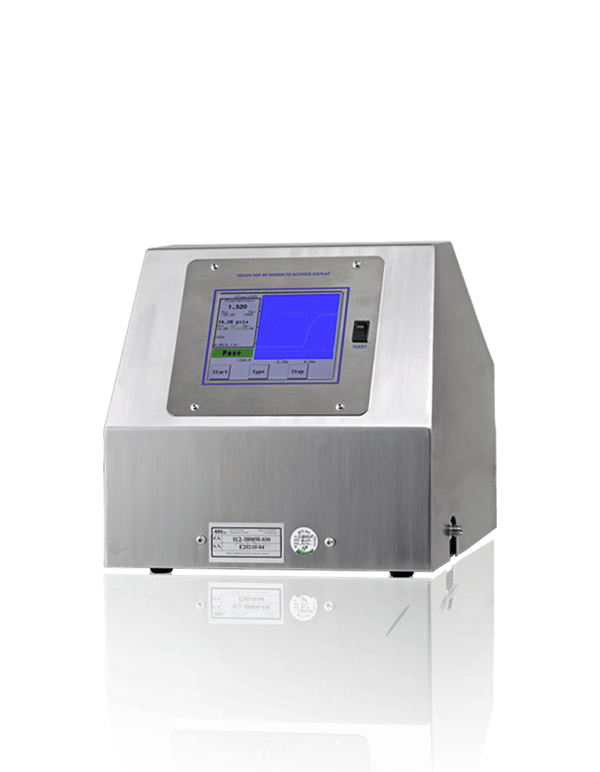
How it Works
At idle the vacuum reservoir and sensor are always exposed to the vacuum source and hold vacuum close to test level. During evacuation steps the chamber opens to the vacuum source. The pouch experiences a pressure differential that is equal to atmospheric pressure-test pressure. The evacuation steps must be long enough for the pressure in the chamber to converge to the pressure in the vacuum reservoir.
During the stabilize step the pouch will leak air into the chamber, creating a pressure differential. This difference takes place between the chamber and the vacuum reservoir. As the pressure differential increases flow through the sensor increases. This will occur until the flow rate through the sensor is equal to the leak rate of the pouch.
Finally, the test step measures the flow rate and compares it to a predefined test rejection limit. A pass/fail decision notification then displays for easy recognition.